Conserto de turbina a gás garante eficiência e performance
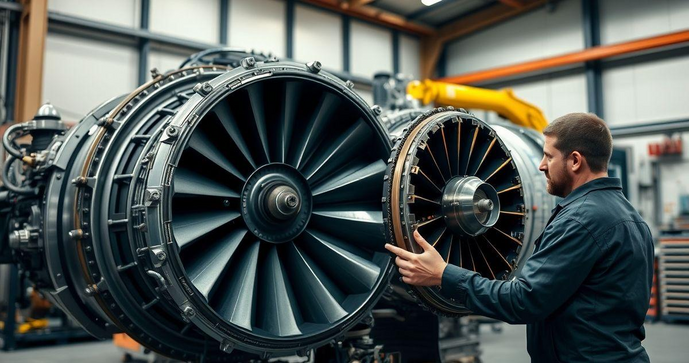
Por: Roberto - 18 de Abril de 2025
Importância do Conserto de Turbinas a Gás na Indústria
O conserto de turbinas a gás é fundamental para manter a eficiência operacional em setores industriais, como geração de energia, petroquímica e transporte.
Essas turbinas desempenham um papel crucial, convertendo energia térmica em energia mecânica, que é utilizada em diversos processos produtivos.
Quando uma turbina a gás falha, a consequência pode ser uma queda significativa na produtividade e um aumento nos custos operacionais devido a tempos de inatividade.
Por isso, é crucial que as indústrias entendam a importância de um conserto adequado e rápido para minimizar os impactos financeiros.
Além da eficiência, o conserto de turbinas a gás também contribui para a segurança do ambiente de trabalho.
Turbinas danificadas podem representar riscos, como vazamentos de gás ou falhas mecânicas, que podem resultar em acidentes graves.
Assim, garantir que os reparos sejam realizados por profissionais qualificados é essencial para mitigar esses riscos.
Outro aspecto importante é a sustentabilidade.
Turbinas a gás bem mantidas operam de maneira mais eficiente, resultando em menores emissões de poluentes.
Investir em consertos regulares ajuda as empresas a cumprirem com as normas ambientais, promovendo um ciclo produtivo mais sustentável.
Por último, a manutenção regular e o conserto oportuno de turbinas a gás podem aumentar a vida útil do equipamento.
Isso resulta em um retorno sobre o investimento mais favorável, permitindo que a empresa maximize seus recursos e mantenha sua competitividade no mercado.
Sinais de Que a Turbina a Gás Precisa de Conserto
Identificar os sinais de que uma turbina a gás precisa de conserto é essencial para garantir a eficiência e operar dentro de padrões seguros. Os primeiros indícios podem ser sutis, mas frequentemente se tornam mais evidentes ao longo do tempo.
Um dos principais sinais a se observar é a diminuição do desempenho. Se a turbina não está rodando na capacidade desejada ou se há uma queda na geração de energia, isso pode indicar problemas internos que precisam ser avaliados.
Outro ponto a se prestar atenção são os ruídos anormais. Sons estrondosos ou vibrações excessivas durante a operação podem ser a indicação de peças soltas ou desgastadas, que requerem atenção imediata para evitar danos mais sérios.
Aumento no consumo de combustível é outro sinal claro. Se a turbina está consumindo mais combustível do que o normal para gerar a mesma quantidade de energia, isso pode ser resultado de ineficiências no sistema que exigem consertos.
Além disso, é importante monitorar as emissões. Se as turbinas a gás estão emitindo mais poluentes do que o padrão permitido, isso não só afeta a conformidade ambiental, mas pode também indicar falhas que necessitam de reparo.
Por fim, a frequência de paradas não programadas é um indicador crítico. Se a turbina está apresentando falhas frequentes que exigem atendimento técnico, é uma forte evidência de que um conserto é necessário para evitar problemas maiores e custos adicionais.
Processo de Diagnóstico de Falhas em Turbinas a Gás
O processo de diagnóstico de falhas em turbinas a gás é um passo crucial para entender e resolver problemas que impactam a eficiência operacional. Este processo deve ser metódico e detalhado, garantindo que todas as causas potenciais sejam investigadas.
Primeiramente, deve-se realizar uma avaliação visual da turbina. Isso inclui a inspeção de componentes visíveis em busca de danos físicos, corrosão ou vazamentos. Uma análise visual pode revelar problemas imediatos e ajudar na criação de um plano de ação para diagnósticos mais aprofundados.
Em seguida, é importante coletar dados operacionais. Informações sobre desempenho, consumo de combustível, temperaturas de funcionamento e vibrações devem ser registradas. Esses dados ajudam a identificar padrões e comportamentos anômalos que podem indicar falhas.
O uso de ferramentas de diagnóstico avançadas, como sensores e sistemas de monitoramento, pode fornecer insights valiosos. Esses dispositivos podem medir diversos parâmetros em tempo real, ajudando a identificar falhas antes que possam causar danos severos à turbina.
Após a coleta de dados, análises específicas devem ser realizadas. Isso pode incluir testes de desempenho que comparam as operações atuais aos padrões de funcionamento ideais. Caso sejam identificadas discrepâncias, uma investigação mais detalhada sobre os componentes envolvidos deve ser feita.
Por fim, a consulta a especialistas e técnicos especializados é fundamental. Eles possuem conhecimento técnico aprofundado e podem aplicar métodos de diagnóstico avançados para determinar rapidamente a natureza das falhas e propor soluções eficazes, garantindo que a turbina retorne ao seu desempenho ideal.
Melhores Práticas para o Conserto de Turbinas a Gás
Para garantir a eficácia e a segurança durante o conserto de turbinas a gás, é importante seguir algumas melhores práticas que otimizam o desempenho e prolongam a vida útil do equipamento.
Primeiramente, sempre realize um diagnóstico completo antes de iniciar qualquer reparo. Compreender a natureza do problema ajudará a selecionar o método de conserto mais apropriado e a evitar intervenções desnecessárias.
Em seguida, utilize peças de reposição originais ou de qualidade equivalente. Peças adequadas garantem que a turbina opere corretamente e minimizam o risco de falhas futuras. Além disso, a utilização de componentes recomendados pelo fabricante assegura a compatibilidade com o sistema.
A documentação de cada etapa do processo de conserto é crucial. Anotar os procedimentos realizados, as peças trocadas e as medições coletadas fornece um histórico detalhado que pode ser útil para futuras manutenções e diagnósticos.
É vital também seguir rigorosamente as diretrizes de segurança durante o conserto. Isso inclui o uso de Equipamentos de Proteção Individual (EPIs), como luvas e óculos de segurança, e a implementação de procedimentos de controle de riscos para evitar acidentes durante a operação.
Por último, a realização de testes pós-conserto é essencial para garantir que a turbina esteja funcionando corretamente. Testar seu desempenho sob condições normais de operação permite detectar qualquer irregularidade antes que possa afetar a produção ou levar a novos problemas.
Manutenção Preventiva para Turbinas a Gás
A manutenção preventiva para turbinas a gás é uma prática essencial que visa garantir a eficiência operacional, aumentar a vida útil do equipamento e evitar falhas inesperadas. Implementar um programa de manutenção regular pode reduzir significativamente os custos e melhorar a confiabilidade da turbina.
Um aspecto crucial da manutenção preventiva é a realização de inspeções periódicas. Essas inspeções devem incluir a verificação de componentes como rolamentos, sistemas de lubrificação e filtros. Inspecionar regularmente essas partes ajuda a identificar desgastes ou falhas precoces, permitindo ações corretivas antes que se tornem problemas maiores.
Outro ponto importante é a limpeza dos sistemas de ar e combustível. A sujeira e os detritos podem comprometer o desempenho das turbinas, por isso é necessário realizar a limpeza regular dos filtros e do sistema de entrada de ar, garantindo que apenas ar limpo entre na câmara de combustão.
A lubrificação adequada das partes móveis também é um aspecto vital. Usar lubrificantes recomendados pelo fabricante e seguir as instruções de frequência de aplicação assegura que as peças operem suavemente e com o mínimo de atrito, evitando desgastes prematuros.
Realizar testes de desempenho rotineiros também deve fazer parte da manutenção preventiva. Medir as eficiências térmica e mecânica ajuda a garantir que a turbina esteja operando conforme as especificações esperadas. Qualquer desvio nos resultados pode ser um sinal de que a turbina precisa de ajustes ou reparos.
Por fim, é fundamental documentar todas as atividades de manutenção. Registros detalhados ajudam a monitorar a saúde da turbina e a avaliar a eficácia das práticas de manutenção ao longo do tempo, permitindo ajustes contínuos no programa de manutenção preventiva.
Escolhendo um Profissional para o Conserto de Turbinas a Gás
Escolher um profissional qualificado para o conserto de turbinas a gás é fundamental para garantir que os reparos sejam realizados com eficiência e segurança. A seleção do técnico ou da empresa ideal pode impactar diretamente a performance e a vida útil da turbina.
Primeiramente, verifique a experiência e a formação do profissional. Aqueles que possuem formação técnica ou engenharia em áreas específicas, como energia ou mecânica, têm um entendimento mais profundo das operações de turbinas a gás. Além disso, a experiência prática em consertos anteriores é um indicativo da capacidade do profissional.
Solicitar referências é uma etapa crucial. Conversar com outros clientes que já utilizaram os serviços do profissional pode fornecer insights valiosos sobre a qualidade do trabalho, cumprimento de prazos e bom atendimento ao cliente. Avaliações e testemunhos podem ajudar na tomada de decisão.
Outro ponto a considerar é a certificação e credenciamento do profissional ou empresa. Certificações de organismos reconhecidos garantem que os serviços serão prestados de acordo com padrões de qualidade. Isso também demonstra o comprometimento do prestador de serviços com a atualização e formação contínua.
Verifique se o profissional possui um seguro adequado. Isso garante que tanto o técnico quanto seu patrimônio estão protegidos durante a execução dos trabalhos. Em situações onde podem ocorrer danos à turbina ou à instalação, esse seguro pode evitar custos significativos.
Por último, discuta os termos e condições do serviço, incluindo prazos, garantias e custos. Ter um contrato claro pode evitar mal-entendidos e garantir que todas as partes estejam alinhadas quanto às expectativas. A comunicação transparente sobre o que será realizado e os custos envolvidos é essencial para um bom relacionamento profissional.
Em resumo, o conserto de turbinas a gás é uma atividade essencial que requer atenção e conhecimento especializado.
Identificar sinais de falha, realizar diagnósticos precisos e seguir melhores práticas de conserto são etapas fundamentais para garantir a eficiência e segurança do equipamento.
A manutenção preventiva também desempenha um papel crucial na maximização da vida útil das turbinas, enquanto a escolha de profissionais qualificados para reparos assegura a eficácia dos serviços prestados.
Investir nessas práticas não apenas melhora a performance das turbinas, mas também contribui para a sustentabilidade e economia a longo prazo na operação industrial.