Guia Completo sobre Reparo de Turbina a Gás
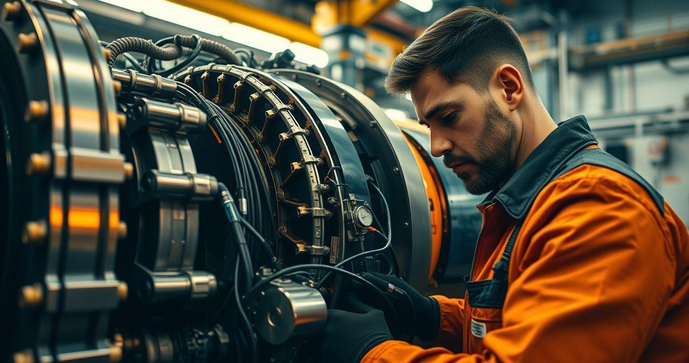
Por: Roberto - 24 de Fevereiro de 2025
Entendendo o funcionamento da turbina a gás
A turbina a gás é um equipamento crucial utilizado em uma variedade de aplicações, incluindo geração de energia elétrica e propulsão de aeronaves. Seu funcionamento básico se dá através da conversão de energia química, proveniente do combustível, em energia mecânica. O processo inicia-se com a queima do combustível, que ocorre em uma câmara de combustão, onde o ar comprimido é misturado ao combustível e inflamado, resultando em gases de alta temperatura e pressão.
Esses gases geram uma expansão rápida que faz com que uma série de lâminas giratórias, ou palhetas, sejam acionadas. À medida que os gases passam pelas lâminas da turbina, a energia cinética dos gases é transferida para a turbina, fazendo-a girar. Esse movimento rotacional é, então, utilizado para acionar um gerador, no caso de uma turbina de geração de energia, ou fornecer propulsão em motores a jato.
Além disso, a turbina a gás opera em um ciclo termodinâmico conhecido como ciclo Brayton, que envolve a compressão do ar, a combustão de combustível e a expansão dos gases quentes. Este ciclo permite que o sistema mantenha uma alta eficiência na conversão de energia. Compreender o funcionamento de uma turbina a gás é fundamental para diagnosticar problemas, realizar manutenções apropriadas e otimizar seu funcionamento.
Principais causas de falha em turbinas a gás
As turbinas a gás, embora altamente eficientes, podem apresentar falhas que comprometem seu desempenho e confiabilidade. Entre as principais causas de falhas, destacam-se o desgaste e a fadiga dos materiais, que ocorrem devido à exposição contínua a altas temperaturas e pressões. Com o tempo, os componentes, como lâminas e cilindros, podem sofrer deformações e rachaduras, levando a falhas funcionais.
Outra causa significativa de falha é a contaminação do combustível e do sistema de lubrificação. Impurezas ou elementos indesejados podem entrar na câmara de combustão, criando problemas de queima e reduzindo a eficiência. Além disso, a falta de lubrificação adequada pode resultar em danos sérios aos componentes móveis, causando falhas mecânicas que interrompem a operação da turbina.
A manutenção inadequada é também um fator importante que contribui para as falhas das turbinas a gás. Protocolos de inspeção e manutenção regulares são essenciais para identificar desgastes ou problemas potenciais antes que se tornem críticos. Ignorar essas práticas aumenta o risco de falhas inesperadas, que podem levar a paradas não planejadas e custos elevados de reparo.
Por último, o design inadequado e a operação fora das especificações recomendadas também podem originar falhas. Sobrecargas, variações extremas de temperatura e condições de operação inadequadas podem resultar em danos significativos aos componentes da turbina. Portanto, compreender essas causas de falhas é fundamental para a implementação de um plano de manutenção proativo que garanta a longevidade e eficiência do equipamento.
Técnicas comuns de reparo em turbinas a gás
O reparo de turbinas a gás envolve diversas técnicas que visam restaurar a eficiência e a funcionalidade dos componentes danificados. Uma das técnicas mais comuns é a soldagem, que é utilizada para reparar fissuras e desgastes em lâminas, caixas de combustão e outros componentes estruturais. A soldagem pode ser realizada com diferentes processos, como a soldagem a arco elétrico ou por fusão, dependendo do material e do tipo de dano.
Outra técnica importante é o recondicionamento de lâminas. Esse processo envolve a remoção de material desgastado e a aplicação de novos revestimentos, como a deposição de metal por explosão ou por spray térmico. Com isso, é possível recuperar a geometria e as propriedades mecânicas das lâminas, garantindo que elas funcionem de maneira eficiente e segura.
A inspeção não destrutiva (IND) também desempenha um papel crucial nas técnicas de reparo, permitindo a identificação de falhas internas sem danificar os componentes. Métodos como a ultrassonografia, raios X e partículas magnéticas ajudam os engenheiros a detectar fissuras e descontinuidades nos materiais, possibilitando reparos direcionados que evitam falhas subsequentes.
Além disso, o balanceamento dinâmico é uma técnica necessária para garantir o funcionamento suave da turbina após um reparo. Isso envolve ajustar o peso dos componentes rotativos para minimizar vibrações e desgastes prematuros quando a turbina retorna ao funcionamento. Por fim, o tratamento térmico é utilizado para restabelecer as propriedades mecânicas dos materiais ao remover tensões internas que podem ter se acumulado durante o uso.
Importância da manutenção preventiva
A manutenção preventiva é essencial para garantir a confiabilidade e a eficiência operativa das turbinas a gás. Ao implementar um programa regular de manutenção, é possível identificar e corrigir problemas antes que se tornem falhas sérias, evitando paradas inesperadas e custos de reparo altos. A prevenção é sempre mais econômica do que a correção, e isso se aplica diretamente às turbinas a gás.
Um dos principais benefícios da manutenção preventiva é a extensão da vida útil dos componentes. Medidas proativas, como inspeções regulares, troca de filtros e lubrificantes, são fundamentais para evitar o desgaste excessivo e a degradação dos materiais. Isso resulta em uma operação mais confiável e reduz a necessidade de reparos complexos no futuro.
Além disso, a manutenção preventiva ajuda a manter a eficiência energética do sistema. Turbinas bem mantidas operam em condições ideais, o que se traduz em um consumo de combustível mais eficiente e menores emissões de poluentes. Isso é particularmente importante em um cenário onde a sustentabilidade ambiental e a redução de custos operacionais são prioridades.
Outro aspecto importante é que a manutenção preventiva contribui para a segurança dos operadores e da equipe técnica. A identificação de problemas potenciais antes que causem falhas catastróficas reduz o risco de acidentes e proporciona um ambiente de trabalho mais seguro. Portanto, integrar a manutenção preventiva à rotina de operação das turbinas a gás é fundamental para garantir uma operação contínua, econômica e segura.
Sinalizando a necessidade de reparo em turbinas
Sinalizando a necessidade de reparo em turbinas
Identificar a necessidade de reparo em turbinas a gás é uma parte fundamental da manutenção proativa. Existem vários sinais que indicam que um reparo pode ser necessário, e a monitorização contínua do equipamento é crucial. Um dos primeiros sinais de alerta é o aumento nas vibrações durante a operação, que pode indicar um desequilíbrio nos componentes rotativos ou desgaste excessivo.
Além disso, mudanças no desempenho da turbina, como diminuição da potência ou aumento do consumo de combustível, são indicadores claros de que algo pode estar errado. Esses sinais podem ser resultados de falhas como vazamentos, contaminação do combustível ou problemas nas lâminas. Portanto, é necessário realizar medições regulares para detectar essas variações.
Os parâmetros de temperatura também são vitais para monitorar a saúde de uma turbina. A elevação inesperada da temperatura em componentes-chave, como a câmara de combustão ou os estágios de recuperação de calor, pode sinalizar problemas sérios que requerem atenção imediata. Sistemas de controle e monitoramento modernos frequentemente possuem sensores que permitem detectar essas anomalias em tempo real.
Por fim, sons incomuns, como ruídos metálicos, estalos ou zumbidos, podem ser um sinal de desgaste ou falha iminente. Esses sons muitas vezes indicam que componentes estão se deteriorando ou se movimentando de maneira inadequada devido ao desgaste. A escuta atenta e a análise regular do comportamento operacional da turbina são essenciais para garantir que os reparos sejam realizados antes que os problemas se tornem mais graves.
Benefícios econômicos do reparo de turbina a gás
Realizar reparos em turbinas a gás traz diversos benefícios econômicos que podem impactar positivamente a operação de indústrias e sistemas de geração de energia. Um dos principais benefícios é a redução de custos operacionais. Ao manter as turbinas em boas condições de funcionamento, é possível evitar paradas inesperadas que resultam em perda de produtividade e faturamento.
Além disso, turbinas bem mantidas operam de forma mais eficiente, reduzindo o consumo de combustível. Isso se traduz em menores gastos com abastecimento, o que é particularmente relevante em cenários onde os preços do combustível flutuam. Uma operação mais eficiente também ajuda a minimizar as emissões de poluentes, contribuindo para a sustentabilidade e, em muitos casos, possibilitando a adesão a regulamentos ambientais mais rigorosos.
Outro aspecto importante é o aumento da vida útil do equipamento. Realizar reparos de forma regular e diligente significa que os componentes da turbina são mantidos em boas condições, o que evita o desgaste acelerado e a necessidade de substituições frequentes. Um bom plano de manutenção e reparo pode prolongar significativamente a vida útil dos ativos, gerando economia a longo prazo.
Por fim, investir em reparo e manutenção preventiva pode aumentar o valor de revenda do equipamento. Equipamentos bem mantidos e com histórico de manutenção documentado são muito mais valorizados no mercado, o que pode ser benéfico para empresas que pretendem atualizar ou expandir suas operações. Portanto, não apenas a manutenção regular é vital para o desempenho imediato, mas também é um investimento econômico inteligente a longo prazo.
Ao longo deste artigo, discutimos a importância do reparo de turbinas a gás, explorando desde o funcionamento do equipamento até as principais causas de falhas e as técnicas de reparo mais eficazes.
A manutenção preventiva se destaca como um componente essencial para garantir a eficiência e a segurança das turbinas, enquanto a identificação precoce de sinais de problemas pode evitar paradas dispendiosas.
Convidamos você a adotar uma abordagem proativa na manutenção das suas turbinas a gás, implementando técnicas de reparo e monitoramento contínuo.
Como você pretende aplicar essas práticas em sua operação? Pense sobre a importância de garantir a longevidade e eficiência de seus equipamentos.