Manutenção de turbinas a gás é essencial para a eficiência do sistema
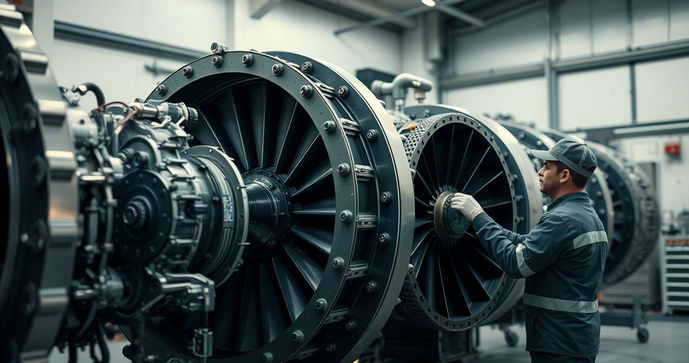
Por: Roberto - 18 de Março de 2025
Importância da manutenção regular para turbinas a gás
A manutenção regular de turbinas a gás é crucial para assegurar o desempenho ideal dessas máquinas. As turbinas operam em condições extremas, exigindo cuidados frequentes para evitar desgastes e falhas sérias.
Uma das principais razões para realizar a manutenção regular é a prevenção de falhas catastróficas. Problemas pequenos, se não identificados a tempo, podem resultar em paradas inesperadas e em custos elevados devido à necessidade de reparos emergenciais.
Além disso, a manutenção adequada garante a eficiência energética das turbinas. Turbinas bem mantidas operam com maior eficiência, resultando em economia significativa nos custos operacionais e diminuição da emissão de poluentes.
A programação de manutenções regulares permite que os operadores ainda realizem avaliações detalhadas de performance, identificando áreas que podem ser otimizadas. A análise de dados coletados durante a operação das turbinas pode fornecer insights valiosos sobre o funcionamento do equipamento.
Outro ponto importante é a duração da vida útil das turbinas. Com a manutenção adequada, os componentes críticos, como os rotores e sistemas de combustão, tendem a ter uma vida útil prolongada, resultando em investimentos mais sustentáveis e duradouros.
Por fim, a manutenção regular contribui para a segurança operacional. Turbinas a gás mal conservadas podem representar riscos significativos, tanto para a equipe quanto para o meio ambiente. Manutenções programadas asseguram que todos os sistemas de segurança estejam funcionando corretamente, minimizando possíveis incidentes.
Principais componentes que requerem atenção
A manutenção de turbinas a gás envolve a supervisão de vários componentes críticos que influenciam diretamente sua eficiência e segurança. Identificar quais partes requerem atenção específica é essencial para um funcionamento adequado.
Um dos principais componentes a serem monitorados são os rotores. Esses elementos giratórios são responsáveis pela conversão da energia do gás em energia mecânica. O desgaste excessivo dos rotores pode comprometer a eficiência da turbina e levar a falhas significativas.
Outro componente vital são as lâminas de turbina, que devem ser inspecionadas regularmente por sinais de erosão ou danos. As lâminas desempenham um papel crucial na maximização da eficiência da energia gerada. Danos a essas lâminas podem resultar em perda de pressão e redução da eficiência.
Os sistemas de combustão também requerem atenção. Manter os queimadores em condições de operação ideais é fundamental para assegurar que a mistura de ar e combustível seja otimizada. Problemas nesse sistema podem levar a queima incompleta e ao aumento das emissões de poluentes.
Partes associadas ao sistema de lubrificação, como bombas e filtros, não devem ser negligenciadas. Uma lubrificação inadequada pode gerar desgaste e aumentar a fricção entre as peças móveis, levando a falhas prematuras e interrupções operacionais.
Por fim, os sensores e sistemas de controle precisam ser regularmente verificados e calibrados. Esses componentes garantem que a turbina opere dentro de parâmetros de segurança e eficiência. Falhas nos sensores podem resultar em decisões inadequadas durante a operação da turbina.
Processo de inspeção e diagnóstico de problemas
O processo de inspeção e diagnóstico de problemas em turbinas a gás é uma etapa fundamental para garantir a operação segura e eficiente dos sistemas. Este processo deve ser realizado de maneira metódica, utilizando técnicas e ferramentas adequadas.
A primeira fase da inspeção envolve a avaliação visual dos componentes da turbina. Técnicos experientes devem examinar sinais visíveis de desgaste, corrosão ou falhas. Essa inspeção pode incluir a verificação de folgas, alinhamento dos rotores e integridade das lâminas.
Em seguida, são realizados testes de performance. Esses testes incluem medições de vibração e temperatura, que ajudam a identificar anomalias no funcionamento da turbina. Monitorar constantemente esses parâmetros permite detectar alterações que podem indicar problemas iminentes.
A análise de fluidos também desempenha um papel crucial. Amostras de óleo e combustíveis utilizados podem ser testadas para detectar contaminação, presença de partículas metálicas ou desgaste. Essa análise ajuda a antecipar falhas em componentes internos antes que se tornem um problema sério.
Além disso, realizar diagnósticos com tecnologia de monitoramento avançado, como sensores de temperatura e pressão integrados, facilita a coleta de dados em tempo real. Essas tecnologias, quando utilizadas corretamente, oferecem uma visão abrangente do estado da turbina e sua operação durante períodos críticos.
Por fim, é essencial documentar todos os achados do processo de inspeção e diagnóstico. Criar relatórios detalhados permite um acompanhamento adequado de tendências de desgaste, facilitando decisões informadas sobre manutenção programada e possíveis intervenções necessárias.
Técnicas de manutenção preventiva e preditiva
As técnicas de manutenção preventiva e preditiva são essenciais para garantir a operação eficiente e segura das turbinas a gás. Ambas abordagens têm como objetivo minimizar falhas e aumentar a durabilidade dos equipamentos.
A manutenção preventiva consiste em realizar serviços programados em intervalos regulares, independentemente do estado atual da turbina. Isso inclui inspeções visuais, limpeza de componentes, trocas de óleo e filtros, e ajustes em sistemas mecânicos. Esse tipo de manutenção é projetado para detectar problemas antes que eles se tornem críticos, assegurando que a turbina funcione em condições ideais.
Por outro lado, a manutenção preditiva utiliza tecnologia avançada para monitorar as condições operacionais da turbina em tempo real. Equipamentos de diagnóstico, como sensores de vibração, temperatura e pressão, fornecem dados contínuos. Esses dados permitem que as equipes de manutenção analisem o estado de saúde da turbina e identifiquem quando uma intervenção é necessária, baseando-se em indicadores objetivos de desgaste e falha potencial.
Uma das técnicas mais comuns na manutenção preditiva é a análise de vibrações. Anomalies nas vibrações podem indicar desgastes nas lâminas ou problemas no alinhamento. Com informações precisas, as manutenções podem ser agendadas apenas quando realmente necessárias, evitando paradas excessivas e prolongadas.
Além disso, a termografia infravermelha é outra técnica útil, permitindo a identificação de pontos quentes nas turbinas que podem resultar em falhas. Esses pontos quentes são indicativos de problemas, como o superaquecimento, que podem comprometer seu funcionamento a longo prazo.
Combinar técnicas de manutenção preventiva e preditiva maximiza a eficiência das turbinas a gás, reduzindo custos operacionais e aumentando a confiabilidade do sistema. Isso proporciona um ambiente mais seguro e sustentável, refletindo um investimento saudável na infraestrutura energética.
Impactos da falta de manutenção nas operações
A falta de manutenção adequada em turbinas a gás pode resultar em uma variedade de impactos negativos nas operações, afetando tanto a eficiência quanto a segurança dos sistemas.
Esses impactos podem se manifestar de diferentes formas, comprometendo a capacidade operacional das turbinas.
Um dos primeiros efeitos da falta de manutenção é a redução da eficiência energética. Turbinas mal mantidas tendem a operar com desempenho inferior, o que resulta em um aumento no consumo de combustível.
Isso não apenas eleva os custos operacionais, mas também aumenta as emissões de poluentes, contrariando esforços de sustentabilidade.
Além disso, a ausência de manutenção regular pode levar a falhas catastróficas. Problemas não detectados, como desgaste em componentes críticos, podem resultar em paradas inesperadas da turbina.
Essas paradas não apenas interrompem a produção de energia, mas também podem gerar custos elevados com reparos urgentes e perda de receita.
A segurança operacional também é uma preocupação significativa. Turbinas a gás não mantidas podem apresentar riscos à segurança dos operadores e do ambiente ao redor.
Falhas em sistemas de segurança, como sensores e dispositivos de desligamento, podem aumentar as chances de acidentes, colocando vidas em risco.
A confiabilidade do sistema é outra questão relevante. Com a falta de manutenção, a confiabilidade das turbinas é comprometida, impactando a reputação da empresa e sua capacidade de atender contratos e demandas do mercado.
Isso pode levar a desconfiança por parte de clientes e parceiros comerciais.
Por fim, o custo total de propriedade aumenta consideravelmente quando a manutenção é negligenciada.
Além dos gastos emergenciais com reparos, existe a possibilidade de custos adicionais com indenizações devido a possíveis danos ambientais ou acidentes causados por falhas operacionais.
Portanto, investir em manutenção regular é fundamental para mitigar esses impactos negativos.
Tendências e inovações em manutenção de turbinas a gás
As tendências e inovações em manutenção de turbinas a gás estão em constante evolução, impulsionadas pela necessidade de otimizar a eficiência, reduzir custos e melhorar a segurança operacional. Diversas tecnologias emergem para transformar a maneira como a manutenção é realizada.
Uma das inovações mais significativas é a integração da Internet das Coisas (IoT) nas turbinas. Sensores conectados coletam dados em tempo real, permitindo um monitoramento contínuo das condições operacionais. Essa capacidade não apenas melhora a eficiência da manutenção preditiva, como também facilita a tomada de decisões informadas com base em dados precisos.
Outra tendência é o uso de análise de big data e inteligência artificial (IA) para prever falhas. Ao compilar e analisar grandes volumes de dados operacionais, algoritmos de IA podem identificar padrões que precedem falhas, permitindo que as empresas agendem manutenções antes que problemas realmente ocorram.
A realidade aumentada (AR) também está se tornando uma ferramenta valiosa na manutenção de turbinas a gás. Técnicos podem usar dispositivos AR para visualizar dados sobre o equipamento em tempo real, sobrepondo informações vitais durante as inspeções e diagnósticos. Isso torna o processo de manutenção mais eficiente e reduz o tempo de inatividade.
Além disso, o treinamento em manutenção está se beneficiando de simuladores e tecnologias virtuais. Técnicos podem adquirir experiência e habilidades em ambientes virtuais antes de trabalhar em equipamentos reais, aumentando a segurança e a eficácia na realização da manutenção.
Por último, os avanços em materiais e tecnologias de reparo também estão contribuindo para a inovação em manutenção. Materiais mais duráveis e técnicas de reparo 3D estão sendo empregados para substituir ou reforçar componentes desgastados, resultando em menos interrupções e um aumento na vida útil das turbinas.
Em suma, a manutenção de turbinas a gás é um aspecto crucial para garantir a eficiência, segurança e sustentabilidade dos sistemas de geração de energia.
Através da implementação de práticas de manutenção preventiva e preditiva, as empresas podem mitigar riscos e evitar falhas catastróficas.
As tendências e inovações, como o uso da IoT, inteligência artificial e realidade aumentada, estão transformando a forma como a manutenção é realizada, tornando-a mais eficiente e proativa.
Investir em manutenção regular e acompanhar as inovações tecnológicas não apenas melhora o desempenho das turbinas, mas também garante um futuro mais sustentável e econômico para a geração de energia.